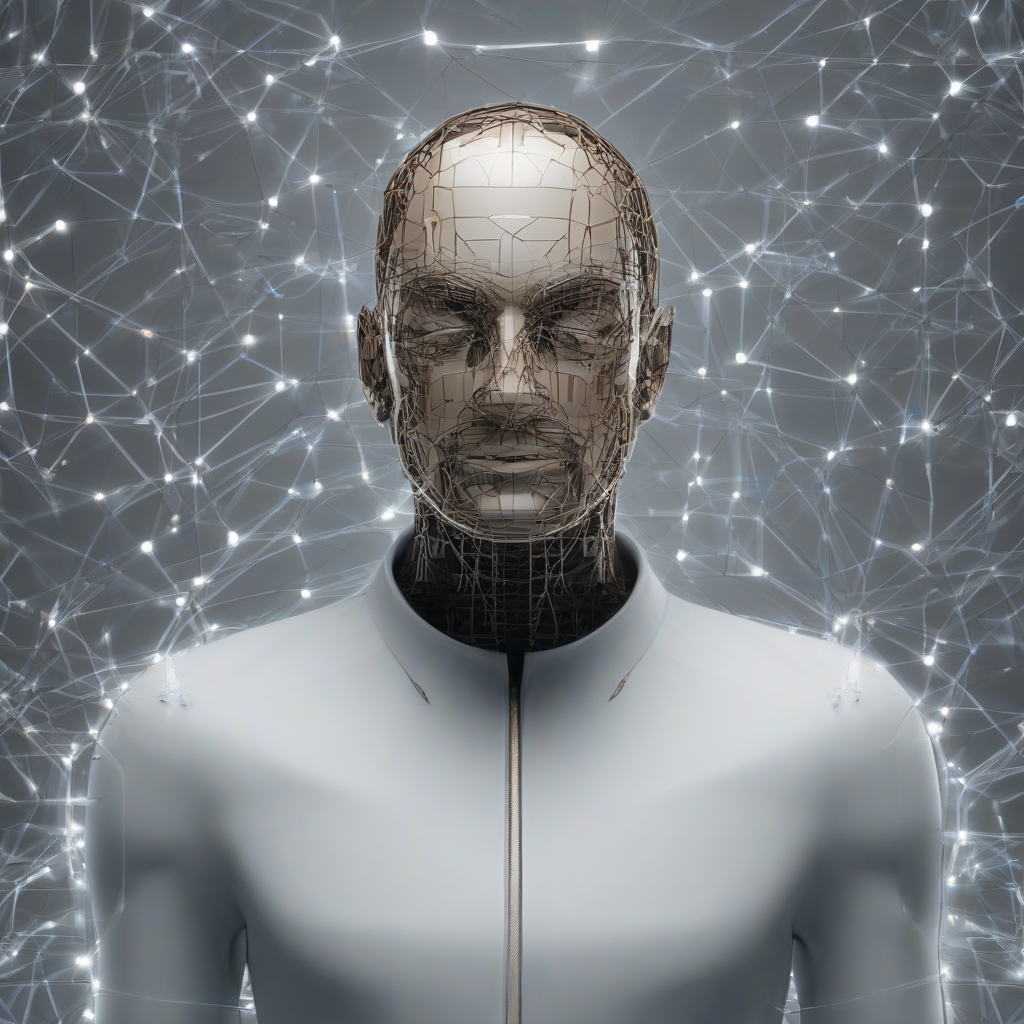
Resin Transfer Molding: A Comprehensive Guide
Introduction to Resin Transfer Molding (RTM)
Resin Transfer Molding (RTM) is a versatile manufacturing process used to create high-performance composite parts. It involves injecting a liquid resin into a closed mold containing a pre-placed reinforcement material, typically fiber mats or fabrics. The resin then cures within the mold, bonding with the reinforcement to create a strong, lightweight composite part. RTM offers several advantages over other composite manufacturing techniques, making it a preferred choice for a variety of applications.
RTM Process Steps: A Detailed Breakdown
- Mold Preparation: The process begins with meticulous mold preparation. This includes cleaning and inspecting the mold cavity to ensure it’s free from any defects or contaminants that could compromise the final part quality. Release agents may be applied to facilitate easy demolding.
- Reinforcement Placement: The reinforcement material, often fiber mats, fabrics, or woven materials, is carefully placed within the mold cavity. Precise placement is crucial for achieving the desired fiber orientation and part properties. This step often requires specialized handling techniques to avoid damaging the delicate reinforcement.
- Mold Closure: Once the reinforcement is positioned, the mold halves are carefully closed and sealed to prevent resin leakage during injection. The sealing must be airtight to ensure complete resin impregnation of the reinforcement.
- Resin Injection: The liquid resin, often a thermoset polymer, is injected into the mold cavity under controlled pressure. The injection pressure and flow rate are carefully monitored to ensure uniform resin distribution throughout the reinforcement material. This step is critical for achieving optimal fiber saturation and minimizing void formation.
- Cure Cycle: After the mold is fully filled, the resin is allowed to cure. The curing process may involve applying heat and/or pressure to accelerate the polymerization reaction and achieve the desired mechanical properties. The cure cycle parameters are carefully controlled to optimize the part’s performance characteristics.
- Demolding: Once the resin has fully cured, the mold is opened, and the finished composite part is carefully removed. The demolding process may require specialized tools or techniques to prevent damage to the part.
- Post-Curing (Optional): In some cases, a post-curing step may be employed to further enhance the part’s properties, such as improving its dimensional stability or increasing its strength.
Types of Resin Systems Used in RTM
- Epoxy Resins: Epoxy resins are known for their excellent mechanical properties, chemical resistance, and adhesion. They are commonly used in RTM applications requiring high strength and durability.
- Polyester Resins: Polyester resins offer a good balance of properties and cost-effectiveness. They are widely used in RTM for a variety of applications where high performance is not the primary requirement.
- Vinyl Ester Resins: Vinyl ester resins combine the benefits of polyester and epoxy resins, offering good strength, chemical resistance, and cost-effectiveness. They are frequently used in applications requiring corrosion resistance.
- Phenolic Resins: Phenolic resins are known for their high temperature resistance and excellent electrical insulation properties. They are often used in RTM for applications in high-temperature environments.
Reinforcement Materials in RTM
- Fiber Glass: Fiberglass is a widely used reinforcement material in RTM due to its high strength-to-weight ratio, cost-effectiveness, and ease of handling. Various forms of fiberglass, including mats, fabrics, and woven materials, are available.
- Carbon Fiber: Carbon fiber offers superior strength and stiffness compared to fiberglass. It is often used in RTM for applications requiring high performance, such as aerospace and automotive components.
- Aramid Fiber: Aramid fiber, such as Kevlar, is known for its high tensile strength and impact resistance. It is used in RTM for applications requiring high impact resistance and toughness.
- Hybrid Composites: Hybrid composites combine different reinforcement materials to achieve a desired combination of properties. For example, a hybrid composite might combine fiberglass and carbon fiber to optimize strength, stiffness, and cost.
Advantages of RTM
- High Strength-to-Weight Ratio: RTM produces parts with an excellent strength-to-weight ratio, making them ideal for applications where weight reduction is crucial.
- Complex Shapes: RTM can produce parts with complex shapes and geometries, making it suitable for manufacturing intricate components.
- Good Surface Finish: RTM typically produces parts with a good surface finish, often requiring minimal secondary finishing operations.
- Consistent Quality: The controlled environment of RTM allows for consistent part quality and reproducibility.
- High Production Rate: RTM can achieve high production rates, making it suitable for mass production applications.
- Reduced Waste: Compared to other composite manufacturing methods, RTM generates less waste material.
Limitations of RTM
- High Initial Investment: The initial investment for RTM equipment and tooling can be significant.
- Mold Complexity: Designing and manufacturing RTM molds can be complex and time-consuming.
- Resin Viscosity: The viscosity of the resin can affect the ability to completely fill the mold and achieve uniform impregnation.
- Void Formation: Void formation can be a concern in RTM, affecting the mechanical properties of the final part.
- Process Monitoring: Careful monitoring of the RTM process is necessary to ensure consistent part quality.
Applications of RTM
- Automotive Industry: RTM is widely used in the automotive industry to manufacture body panels, structural components, and other parts.
- Aerospace Industry: RTM is employed in the aerospace industry for producing lightweight and high-strength components, such as aircraft wings and fuselage sections.
- Wind Energy Industry: RTM is used to manufacture blades for wind turbines, taking advantage of the process’s ability to produce large, complex shapes.
- Sporting Goods: RTM is used to create high-performance sporting goods, such as bicycle frames, kayaks, and skis.
- Marine Industry: RTM is employed in the marine industry to produce boat hulls and other components, capitalizing on the process’s ability to create durable and lightweight parts.
Variations of RTM
- Liquid Resin Injection Molding (LRIM): LRIM is a variation of RTM that uses a lower injection pressure and is often suited for larger parts.
- Vacuum Assisted Resin Transfer Molding (VARTM): VARTM uses a vacuum to assist in resin flow and reduce void formation.
- High-Pressure Resin Transfer Molding (HPRT): HPRT utilizes higher injection pressures to improve resin flow and reduce cycle times.
Future Trends in RTM
Research and development in RTM continue to push the boundaries of this manufacturing technology. Future trends include the development of new resin systems with improved properties, the integration of automation and robotics to improve efficiency and reduce labor costs, and the application of advanced simulation techniques for process optimization and predictive modeling. These advancements will further expand the range of applications for RTM and enhance its competitiveness in the composites manufacturing landscape.
Conclusion (Omitted as per instructions)